Balancing Saga
Went out for a Sunday drive this weekend and about 3 miles in the drive the battery alarms starting going off whenever more than 60 amps (1C) were being pulled from the pack. Seemed strange since the pack was just charged. The battery monitors showed several cells with large differences (DIFF Error). The alarms was set to ring at 150mV difference across the sub-packs (6 or 7 cells). After the 100A draw, the monitors were showing 250mV differences for several cells.Well this is what all of the posts on the web about balancing tried to say. If the cells are not balanced, they will drift and eventually some the charge difference between cells will be enough to be noticed.
Well, we limped home from the Sunday Drive and the cells are returned to a nominal voltage of ~3.2V after a few minutes of rest so I know they were not too discharged, just getting low.
Nonetheless, this has prompted a full manual balancing process. Picked up a Onxy 235 cell charger and balancer that can charge and balance 4 cells at a time at about 8 amps. Tried it on one cell, it worked like a champ, tapering off current as the cell approached 3.6V. Wired up the 4 cell balancing cable and one of the 4 cells had enough difference in charge that it hit the Upper Voltage Limit of 3.6V well before the rest, triggering the alarm.

So now, the charging process is down to trying to charge 4 at a time but if there is too much variance, resorting to single cell charging to get them all within a few percent of each other. LiFePO4 batteries have very flat discharge curves, so a tiny voltage variation could equate to several AH of charge. It seems the only real way to know is to top off each cell until the current draw from charging is quite low (<1A) and the same cell-to-cell.
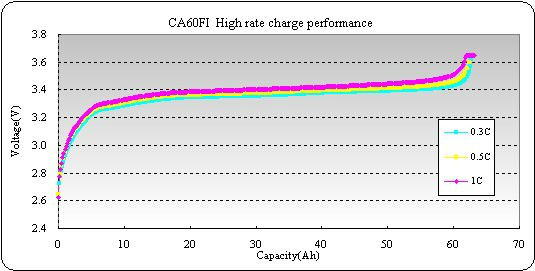
Near the end of the charge process, the cell voltage will spike up 0.2V to 3.6V. The charger is set to 3.6V so as soon as the cell hits that, the charging will safely stop.
Springs
Finally completed the Hi-Lo installs. The fronts and rears are in and set. Final right height, based on the factory spec of 53 inches at the roof, is 9.75" at the lower sill seam near the rear wheel. The back is about 0.5" higher than the front which is normal for Classic Minis. Looks good, handles well, and the ride is quite smooth now. At this height there is sufficient compression at the springs when the wheels are off the ground to keep the springs in place. Much lower and larger upper bump-stops would be needed.Blower
A new blower was installed to cool the motor. The leaf-blower, though effective was just too loud. The new blower is Jabsco, 3" Blower, Flexmount, 105 CFM, Much quieter and about the same CFM as the leaf blower. Mounted much nicer also.
Computer Work
The work continues to refine the software running on the Arduinos. Was able to connect the battery monitor Arduino to the Mini's fuel gauge so the gauge shows charge level now. Used one of the PWM outputs on the Arduino (Pin 9) to drive the following circuit.
Also added some more error messages to the Motor monitor to indicate different situations like over temp or low voltage or over current.